
We have a few options when we exchange/collect redundant bins. We sometimes bring our mobile shredder to a site to shred the bins into 20-25mm chips and bagged into tonne bags, or load onto our trailers to be shipped to our recycling partner, where they are checked prior to feeding into one of the granulation machines, the resultant chip is processed through the wash plant prior to blending and compounding into a new pellet for supply to the manufacturing industry for the production of an array of containers and transit packaging through to new wheeled bins.




To date we have recycled over 5,000 tonnes of HDPE
that's half a million bins, picked up, recycled & made back into wheeled bins
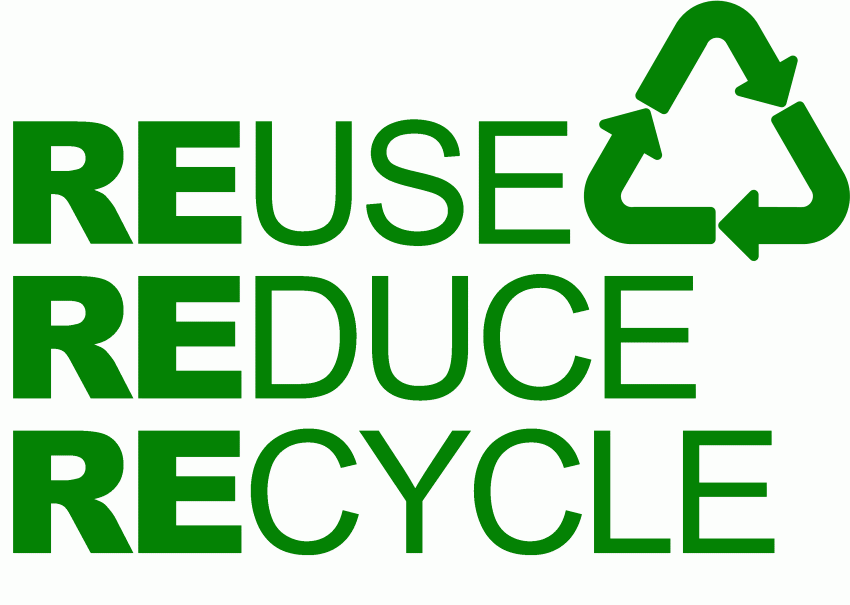
We also reuse a high proportion of the redundant bins. When we have collected the bins from the residents houses, we bring them back to the depot where they are loaded onto a waiting trailer, they then are transhipped to our processing plant. The bin stacks are removed from the trailer. They are then fed straight into the robotic de-branding process. This process is a fully automated robotic cell specifically designed to permanently remove any previously embossed logo’s. The end result of this process is a blank wheeled bin.
The specifically designed robotic bin washer, incorporates 2 industrial robots working in tandem, quickly and efficiently washing the bin to the required standard for reuse.
After both automated stages, each bin is quality checked for cleanliness and free of any logo’s/markings. Each bin is re-stacked including wheels and axles, ready for shipping.


